Turbocharging manufacturing operations with edge computing
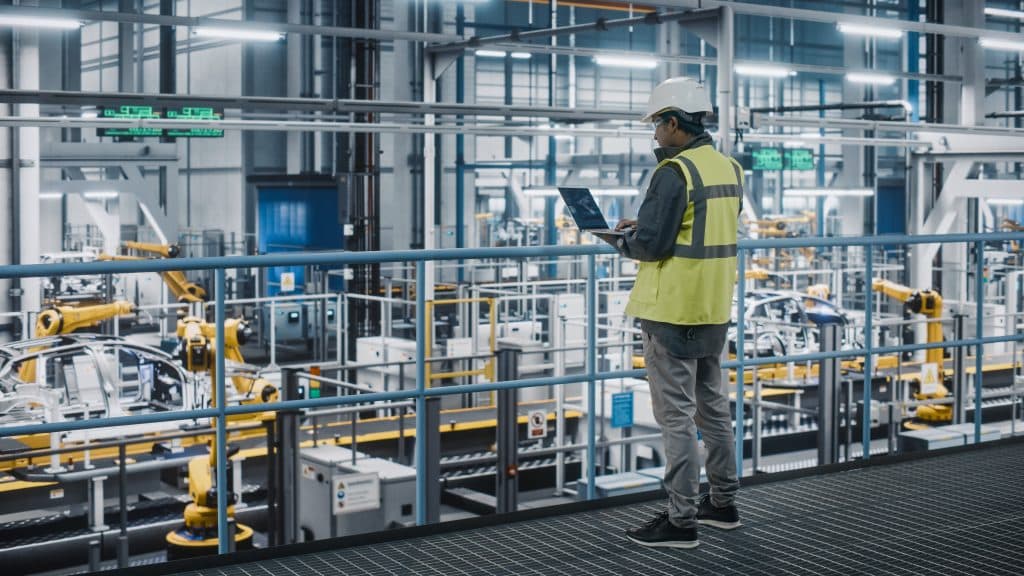
Edge computing reduces bandwidth use and latency by bringing computing as close to the data source as possible. It involves running operations locally, on an IoT device, point of sales (POS) systems, vehicles, or sensors. This emphasis on location is why edge computing is going to be key to turbocharging manufacturing operations.
Why is Edge Computing critical in manufacturing operations?
By 2025, 75% of enterprise-generated data will be created and processed outside the cloud and other centralized data centers. Unlike cloud computing, edge computing allows manufacturers to implement automation across supply chain processes and the factory floor. Instead of sending the information to a server for response or analysis, it brings machine-to-machine communication closer to the data source.
Out of 128 manufacturing decision-makers who participated in a 2020 “Edge Computing in Manufacturing” survey jointly conducted by IDC, Lumen, and Microsoft, 56% committed to implementing edge computing pilots by 2022.
Manufacturers can use edge computing to:
- Track automated machine cycles
- Monitor flow through pipes
- Scan sheet metal to detect fatigue
- Improve overall low latency
Generating, analyzing and acting on real-time data offers profound benefits on the factory floor. It improves overall product quality, predicts maintenance with accuracy, and reduces downtime, resulting in lower overall costs, increased throughput, reduced waste, and higher yield.
Edge computing use cases in manufacturing operations
Industry 4.0 initiatives have advanced from pilot stages to mass deployments, leading to speed limitations in data transmissions. Edge architecture can provide the bandwidth, speed, and resilience required to support fully automated factories and advanced networks of industrial IoT (IIoT) devices.
Edge computing can help manufacturers improve their productivity and efficiency in the following ways:
- Defect detection: Detecting defects is an indispensable element of the manufacturing process. Assembly lines that produce millions of units try to catch defects in real-time. Edge computing devices, combined with computer vision technology, can detect faults immediately, make split-second choices, and alert quality controllers. In turn, efficiency increases and waste decreases.
- Predictive maintenance: Using sensor data to track manufacturing trends and monitor production patterns to predict machine downtime is known as predictive maintenance. Sensors installed on equipment scan for defects in real time. They notify management when a machine needs repair, ensuring minimal downtime. Manufacturers can combine edge computing, artificial intelligence (AI), and sensor data to analyze equipment conditions and avoid unforeseen expenditures. For example, computer vision AI can help detect pipeline corrosion in chemical facilities and alert the maintenance staff before the damage worsens.
- Regulatory compliance: Combined with edge computing and sensor data, computer vision technology can help companies monitor products in real time, helping them identify safety issues or flaws. This can help manufacturers comply with industry regulations, such as quality assurance in the automobile welding process.
- Yield improvement: Edge computing, AI-driven digital twins and sensor data can help modify manufacturing parameters and recalibrate machines in real-time. This results in a better final It eliminates the need to send to a central location for analysis. Using edge computing, on-site sensors can make real-time decisions to boost yields. This is vital in food processing plants, where the exact quality and quantity of the components are crucial in the manufacturing process. Pharmaceutical manufacturers are getting higher drug yield and reduced wastage due to scrapped tablets.
- Reduce latency and costs: Manufacturers often deploy digital twin technology to simulate the performance metrics, environmental conditions, etc., of their factory floor. Thousands of sensors installed to measure these parameters generate massive amounts of data. Moving this continuous data stream to and from a cloud data center can result in latency, network bandwidth constraints, and substantial costs. Edge computing can process and analyze this data close to the source, enabling digital twins and vastly reducing reaction times.
- Improved business outcomes: Manufacturers construct 3D digital twins of their products to reduce constraints on team locations. It allows their engineers and designers to work with each other in real-time virtual reality. Manufacturers deploy process digital twins supported by edge computers to successfully reduce overall machine set-up time. Edge computing hardware and software devices help 3D computer-aided design (CAD) models seamlessly integrate with factory operations, affecting business outcomes in real-time.
Edge computing offers unique benefits over conventional models, where on-premises data centers provide centralized computing power. It helps companies improve the use & management of their physical assets to create interactive & new human experiences.
By some estimates, analysts expect edge computing to generate revenue of more than $34 billion by 2030. Edge computing, combined with technologies like digital twins and computer vision, promises to transform manufacturing automation in the coming years.
About the author
Sunil Kardam leads the logistics and supply chain business unit at Gramener Inc, a design-led data science company. He advises clients on how to formulate a data strategy, identify their most impactful data science use cases in line with business objectives, and implement custom data and AI solutions.
A certified member of the Association of Supply Chain Management (ASCM), Kardam has a sixteen-year track record in the supply chain and logistics domain.
DISCLAIMER: Guest posts are submitted content. The views expressed in this post are that of the author, and don’t necessarily reflect the views of Edge Industry Review (EdgeIR.com).
Article Topics
edge analytics | Gramener Inc. | Industry 4.0 | IoT | manufacturing
Comments