How Phizzle is helping pharma companies wrangle data from edge devices—and a big ROI
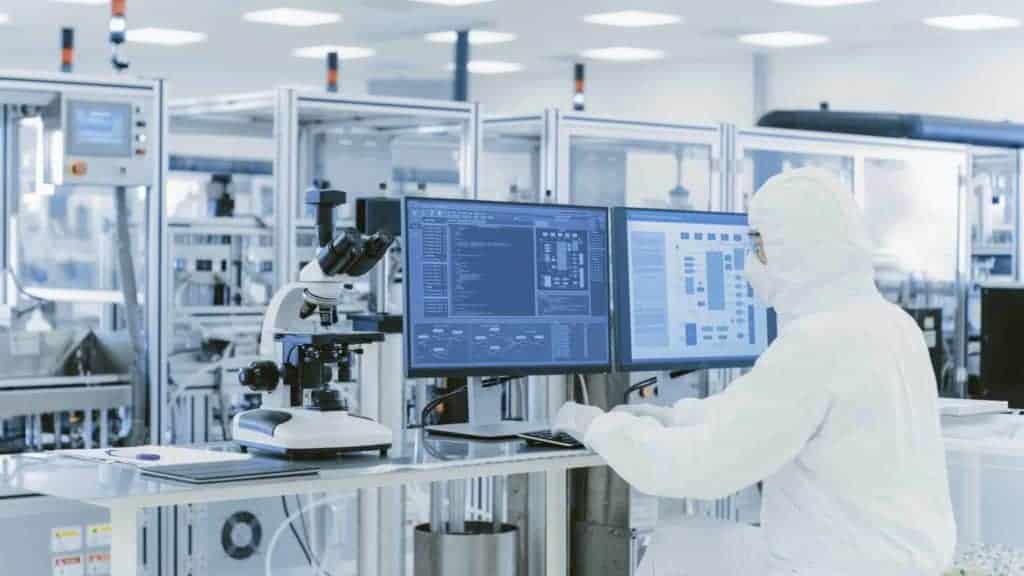
Pharmaceutical manufacturing is always a very serious business. That point was driven home when Johnson & Johnson experienced problems making its Coronavirus vaccine at a Baltimore, MD plant in April that resulted in the contamination of 15 million doses. Monitoring the production process is critical, and new IoT solutions are looking to make that process easier.
Case in point: Phizzle, a provider of IoT software for edge computing, which recently introduced the EDGMaker Digital Air Series. The software is used to remotely operate particle counters in scientific data applications such as pharmaceutical manufacturing. The big benefit of connecting these devices? Pharma companies are finally able to manage particle counters of a variety of makes and models and the process of digitization has enabled them to standardize the process of collecting data—all while reducing the amount of manual labor needed to operate machines. Another benefit: fewer data entry errors and the ability to normalize data across disparate devices, making it easier to measure production quality over time.
Producing drugs requires strict monitoring of the cleanliness of the manufacturing process. Pharmaceutical. One part of the quality control process: pharmaceutical manufacturers are required to regularly measure air quality using particle counters. According to Phizzle, this has been a time-consuming and manual process that typically requires an average of 1.5 to 1.8 lab technicians to handle each particle counter as they move devices around the plant to measure air quality. Phizzle said that EDGMaker has already been used in the FDA-required manufacturing practices of a top-five U.S. pharmaceutical manufacturer, resulting in up to a 45% reduction in labor costs per particle counter while also reducing the risk of compliance errors.
Edge Industry Review interviewed Phizzle executives Ben Davis, CEO, and Jeff Cristee, Chief Revenue Officer, to talk more about the use of edge computing in manufacturing. This interview has been edited for length and clarity.
Q: Can you tell us about the problem Phizzle is trying to solve, and how you came across this challenge in pharmaceutical manufacturing?
BD: “Our philosophy and our DNA has always been to look, analyze, and capture lots of data and make decisions on what to do with that data very quickly.
The three main value points of our edge solution are the ability to run in a resource-constrained environment, the ability to look at lots of data, and then the ability to execute on preconfigured decisions with very low latency down to sub-millisecond timeframes.
And so while we thought that we would penetrate the transportation and manufacturing, CNC manufacturing verticals, we actually ended up solving a pretty big problem in pharmaceutical manufacturing. That problem is that there is a wide variety of scientific device instrumentation in terms of function and age, which means that in pharmaceutical manufacturing, there are many different vendors of machines that are part of the manufacturing process. Because these machines have different control paradigms, different communication protocols, it often requires a lot of labor to operate these machines. What we’ve done is create a platform that provides a homogeneous environment to remotely operate all of these machines as if they’re one. We’ve streamlined all of the variable degrees of controlling these machines.
Our first customer [in pharma] was through the Cisco relationship. And so we formalized a partnership with Cisco, who needed some advanced edge compute solutions.
Q: Can you provide some more detail about the deployment and solution?
JC: Our customer has 10,000 scientific devices throughout their global manufacturing plant [footprint]. The scientific devices monitor all sorts of information that are required and validated in their manufacturing process by the FDA for them to be compliant. Some measure the pH, some measure viscosity of the ingredients that actually are in the medicine, but some just measure the environment. And they have to produce within that environment.
Our first customer has at least 1500 [air particle counters] globally. For every one of these we automate, they’re told us they’re saving more than $100,000 in operating expense per device.
The second benefit is data integrity. The customer says “We now immediately know what the records say. But not going through a manual process, we get rid of all that paper and all of that signing; we can sign that digitally through a console all operated from one console. And we sign that data and store it immediately in the LIMS. If a test is out of compliance, we know immediately instead of waiting.”
Q: We’ve read a lot about using AI for the drug discovery process. But hearing about how manual the manufacturing process still is, is sort of shocking and amazing. How important is being able to gather and manage data from edge devices to digital transformation efforts?
BD: We give a complete digitization of a very manual process, complete with a digital sign-off and management process. We’re completely taking the paper out of the picture, taking out all the manual steps in…one of the last remaining industries to have not been completely disrupted by the internet and digitalization.
These processes for pharma manufacturers go back many years and are well established; they understand the compliance issues and how to deal with them. They work and generate billions and billions of dollars in profit. Despite how manual it is, it’s very profitable. The ROI has got to be compelling to change something that is well established and proven. And I think that’s the magic behind our software is that the ROI is very apparent, and it’s pretty immediate and it helps defend against compliance and certification issues.
HP selects Saguna to deliver edge incubation lab to Globe Telecom
Article Topics
Cisco | IIoT | Industry 4.0 | manufacturing | pharmaceutical | Phizzle
Comments