Bringing SCADA to the Edge for Industrial Automation
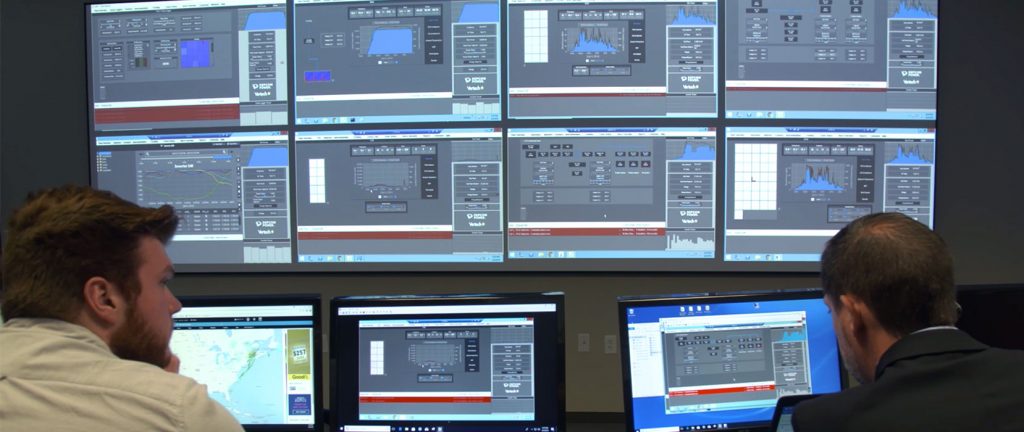
This is a guest post by Cole Wangsness, a Solutions Specialist at OnLogic.
Industrial automation is the use of technology to perform an industrial process or procedure with minimal human intervention. Industrial automation systems can be very complex, consisting of a large number of devices working in synchronization with automation technologies. To help with automation, Supervisory Control and Data Acquisition (SCADA) systems are used to facilitate the control and intervening functions, such as setting production targets and monitoring various parameters.
What is SCADA? SCADA is a combination of hardware and software that allows users to:
– Monitor and control industrial processes both locally and remotely.
– Acquire, process, and record data.
– Interact with local machinery through HMIs (Human Machine Interfaces) and PLCs (Programmable Logic Controllers).
SCADA systems work by connecting the local sensors, devices, and PLCs—which collect datasets, known as Tags—to an on-site server or remote/virtual machine. Data can be saved to a historical database so that it can be analyzed later. Users interact with the SCADA system locally to control processes through operator workstations, HMIs, or directly on the SCADA server.
The advantages of SCADA at the edge
A SCADA system brings more visibility to users to make informed decisions. For example, a plant supervisor at a soft drink bottling plant wants to be able to view all production lines, improve uptime, and reduce operational inefficiencies based on the plant’s current performance. To accomplish this, they need tags from each production line. With a SCADA system, the line supervisor would receive an alert when a filling station’s nozzle pressure has gone down by 20%, increasing cycle time by five seconds. The line supervisor can quickly send a technician out to replace the damaged nozzle and bring the line back up to full capacity. Using a SCADA system, the plant supervisor was able to diagnose and fix the issue before it led to process bottlenecks in later stations or brought the whole line down due to a critical part failure. Implementing an edge computing solution allows for these type of improvement or preventative maintenance opportunities to be identified and acted on in real-time.
Questions to ask when considering using SCADA at the edge
What am I looking to accomplish?
– A SCADA system can meet a wide variety of needs, so it is important to define your project goals and KPIs from the start. Beyond plant control and monitoring, do you want to reduce costs related to maintenance? Reduce downtime? Improve plant reporting?
What machinery will I need to monitor to accomplish my objectives?
– Am I installing new machinery or upgrading existing machinery? Can I communicate directly with the machinery via an industrial protocol like Modbus TCP/IP or do I need to integrate PLCs to communicate with the machinery and sensors like Allen Bradley’s CompactLogix or Siemen’s S7 Series?
What type of hardware will I need to deploy?
– Do I need a computer that can run 3+ monitors in the control room for overall plant supervision? Do I need an all-in-one panel PC for an HMI so my production line operators can interact with machinery directly on the line? Do I need a rugged edge computer with a 4G LTE modem to send data back over MQTT from my field site?
Who are my stakeholders for this project?
– Engineering, IT, OT, and other relevant departments should be involved to ensure a smooth integration process.
Do I have the right people on my team to support a SCADA integration?
– If this is your first time implementing a SCADA solution, your company might not have the necessary knowledge base to support it. Many end-users of SCADA systems work directly with an approved solutions integration partner to help tailor a solution to the unique demands of a given project.
Leveraging Software for SCADA
Leveraging software for SCADA means finding a hardware-agnostic platform that connects all the devices on your plant floor including different PLCs, databases, and PCs that you need. Also seek out solutions that have powerful built-in visualization and reporting tools so decision makers can make the right decision at the right time.
One of the inherent risks of IIoT (Industrial Internet of Things) applications is that many systems require an internet connection to function properly. Look for software that can activate independently should a network connection go down.
Example Use Case: Oil and Gas Projects
Let’s say you have 50 well sites for natural gas extraction. How much does it cost each time a technician’s truck rolls to update IT equipment at one of those sites? You could create a local HMI for your operators that doesn’t depend on a network connection. With the right equipment, you could set up a SCADA solution to send trending data back over MQTT via 4G LTE using a reliable, wide-temperature rated Rugged PC with an integrated modem. With the ability to remotely monitor each site in real time, your techs can spend more time on critical maintenance and less on IT equipment upkeep.
Industrial Edge PCs for SCADA
A quick word on hardware for SCADA deployments. Most automation solutions can’t accommodate the downtime caused by unreliable IT equipment, but it’s increasingly common to find SCADA applications outside of carefully controlled environments (see the example above). Industrial PCs are resistant to dust, temperature, shock, vibration, and variable input power, making them ideal for this breed of advanced SCADA at the edge. Features like internal 4G LTE modems for remote communication, PoE+ ports to run a camera or other powered peripherals and solid-state components to reduce the chance of failure over prolonged usage periods all make this type of specialized hardware ideal for SCADA deployments. If you’re setting up a SCADA solution at the edge, the right choice in hardware can make or break a project, so it is important to consider requirements well in advance.
The breadth of automation applications is limitless, and SCADA is often the unsung hero in ensuring each element in the process communicates effectively. The combination of hardware, software, and application architecture can be daunting to conceptualize, but finding the right solution has the potential to completely revolutionize the way you do business.
About the Author
Cole Wangsness is a Solutions Specialist at OnLogic. OnLogic is a global industrial computer manufacturer that designs highly configurable, solution-focused computers engineered for reliability at the IoT Edge. Cole works to connect OnLogic clients with the right hardware solution to their technology challenges. When not working, he enjoys researching new technologies and tinkering with computers.
DISCLAIMER: Guest posts are submitted content. The views expressed in this blog are that of the author, and don’t necessarily reflect the views of Edge Industry Review (EdgeIR.com).
Article Topics
device edge | edge gateway | IIoT | industrial automation | industrial edge | Industry 4.0 | OnLogic | systems integration
Comments